Boiler maintenance reduced with insulation jackets
We removed and replaced the insulation on Twinwoods’ biomass boilers to carry out routine maintenance. It was a time consuming process because each one had to be replaced with new insulation. Our ContraFlex® jackets delivered the solution required because they are rapid to remove and replaceable.
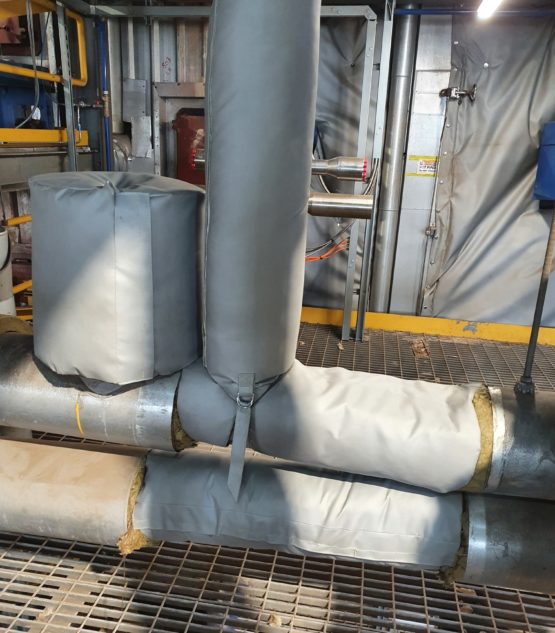
The highlights
Time saving
Removing the boiler insulation used to take the customer a week and involved six people. In contrast, removing the ContraFlex® jackets will take a team of two people around half a day.
Cost savings
The previous boiler insulation had to be disposed of after it was removed. Our ContraFlex® jackets can be removed and replaced each time, saving disposal costs and reducing environmental impact.
Maintenance
ContraFlex® jackets have a grey silicon cover that can be wiped down as required. This makes them easy to clean - a significant benefit in the dusty atmosphere of a biomass boiler plant.
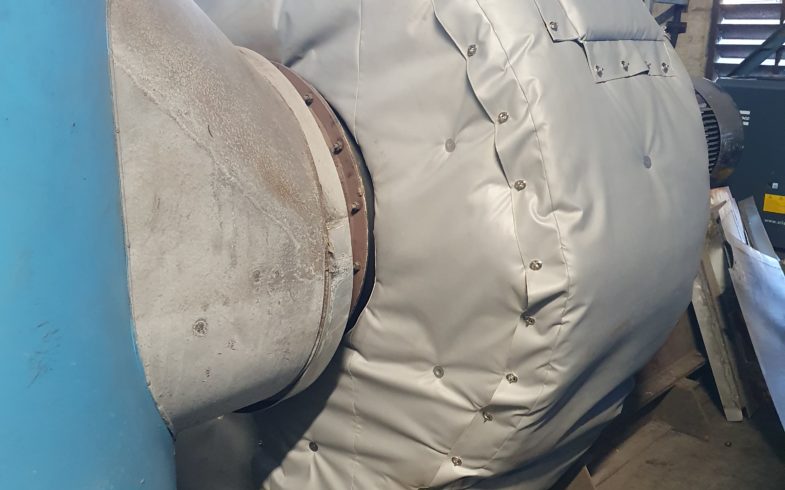
Biomass boiler maintenance time and costs reduced
The biomass boilers at Twinwoods undergo maintenance works every 12 to 18 months. However, the work was complicated by the insulation on the boilers. The insulation on the boilers needed to be removed before maintenance work could begin – a time-consuming task that involved a team of several people. Therefore, maintenance was taking longer than was acceptable, costing time and money. In contrast, the ContraFlex® jackets can be removed by a team of two in less than a day.
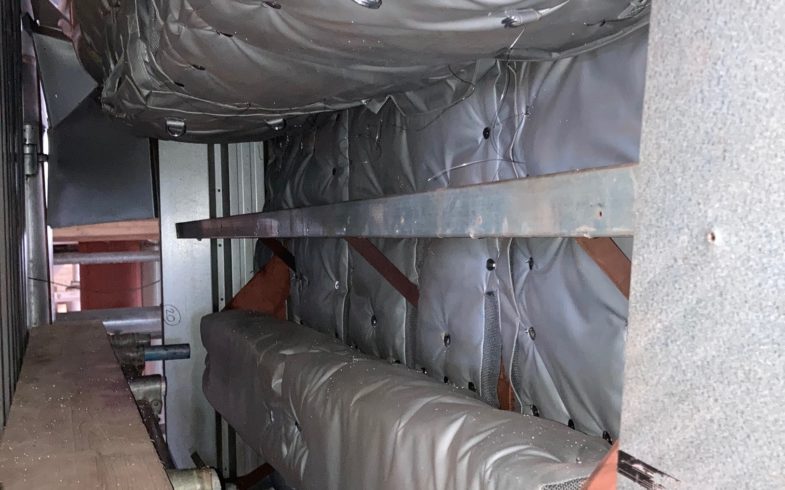
Cost and environmental savings realised
The previous insulation was time-consuming to remove and could not be reused. This meant the old insulation needed to be disposed of and new insulation purchased each time, which resulted in increased costs. There were also the environmental costs of this activity to consider. In contrast, ContraFlex® jackets can be removed and then reused, reducing lifecycle costs and environmental impact.
Other highlights
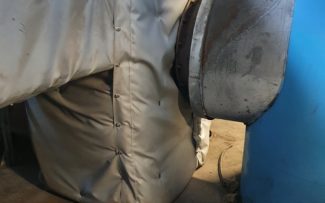
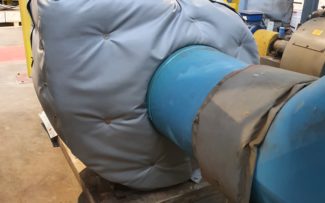
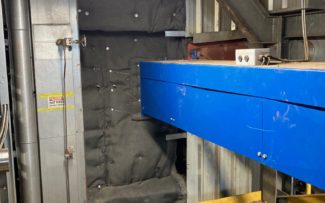
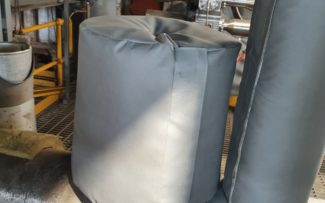
Share your protection challenge
Do you need to protect equipment in an extreme operating environment? Let us discuss how we can help.
Get in touch