ContraFlex® installs insulation jackets at sulphur plant
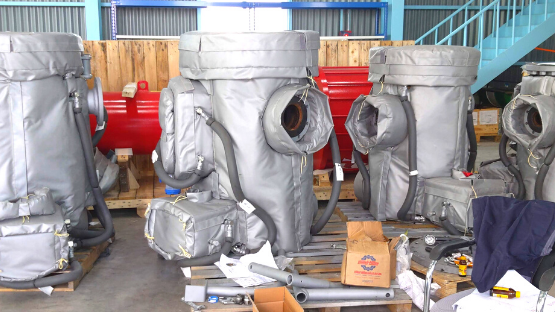
The highlights
Dedicated team
Our local team in South Korea conducted a full site survey, to capture all measurements accurately.
50mm
Our recommended solution was to install 50mm of insulation securely fastened with Velcro type hooks and loop tape.
Maintenance
We incorporated inspection hatches in the jacket system for easy access.
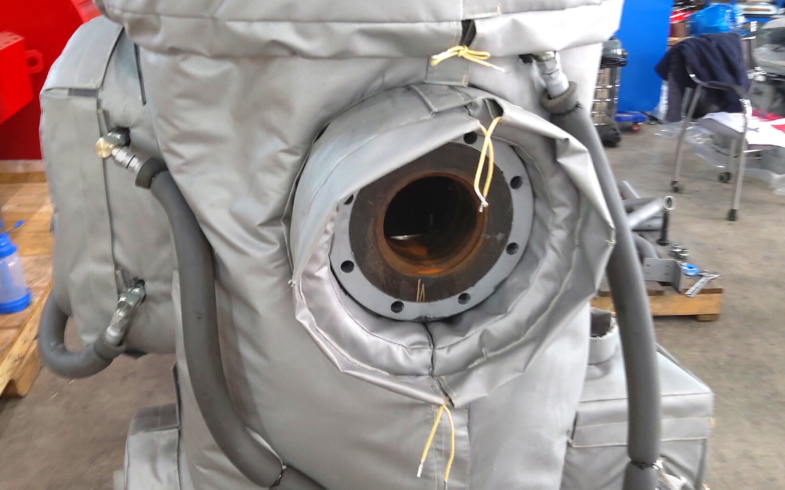
The challenge
Our customer who operates one of South Korea’s largest sulphur plants required a solution that would:
• Ensure the sulphur did not solidify within the lines or equipment
• Ensure that noise levels were kept at an acceptable level to protect their employees.
They specified that they wanted a jacket solution that was quick and easy to fit and which once installed would provide their maintenance team with access to key parts of four sulphur trap units.
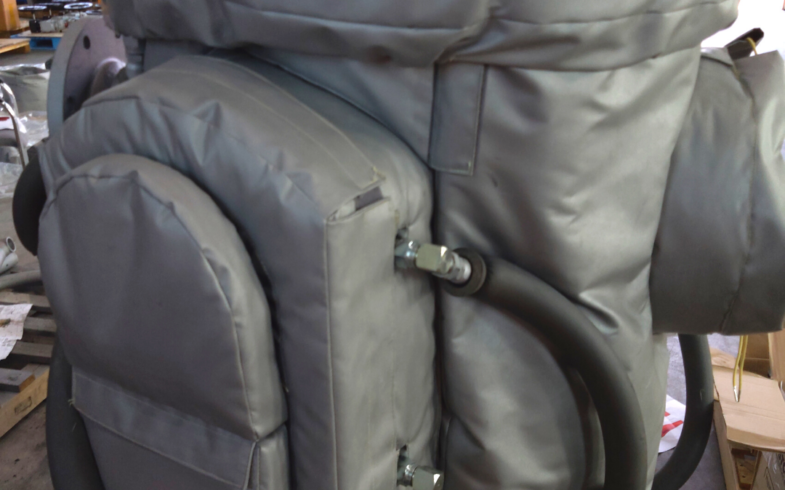
Our solution
As we could not obtain 3D models, our local team in South Korea conducted a full site survey, to capture all measurements accurately to ensure that the bespoke jackets manufactured would be the correct snug fit. The solution required thermal and or acoustic jacket insulation – our ContraFlex® jacket solution is specified for heat conservation to a maximum process temperature of 158°C. Due to the nature of the infill material, the system also provides a level of acoustic protection as standard, which helps to mitigate noise exposure risk to employees.
Our recommended solution was to install 50mm of insulation securely fastened with Velcro type hooks and loop tape. This type of fastening makes the system quick and easy to fit, and enables easy access if the equipment requires any maintenance checks.
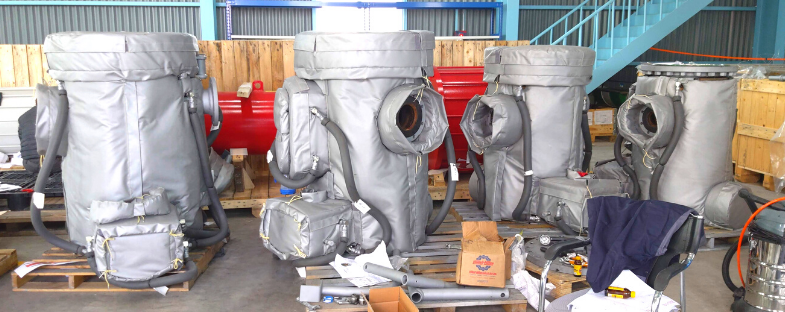
The results
Our customer had specified they wanted their maintenance team to be able to safely remove sections of the system to check on vital parts of the equipment. During the design phase, we incorporated inspection hatches in the jacket system for easy access, whilst ensuring maximum protection from the hot surfaces and minimising equipment heat loss.
We recommend installation by our experienced team on site or at customer’s fabrication yard which is where this installation took place to ensure a smooth and efficient site experience.
Our jacket system was installed on-time and within project budget – we achieved this for our customer by working with them to deliver a full-turnkey solution which included, site-survey, design and installation supervision.
Share your protection challenge
Do you need to protect equipment in an extreme operating environment? Let us discuss how we can help.
Get in touch